"I don't think I'll run out of people who are willing to fly the spaceship any time soon."
On Monday, Virgin Galactic announced that it will conduct its next commercial spaceflight, Galactic 03, as early as September 8. This will be the company's third commercial spaceflight, and it will carry three as-yet-unnamed passengers who bought their tickets on the company's space plane back in the early 2000s.
Should the flight occur in early September, it will mark the company's fourth spaceflight in four months, an impressive cadence after a fairly long downtime. Such a flight would also cement Virgin Galactic's leadership in the suborbital space tourism race with Blue Origin, which has been grounded for nearly a year after a launch accident with its New Shepard System nearly a year ago.
To understand why there was such a long downtime after Sir Richard Branson's flight on Virgin Galactic in 2021 and to learn how the company has reached a monthly flight cadence, I recently had a long interview with Mike Moses, the company's chief of operations and president. Moses came to Virgin Galactic in 2011 from NASA, where he worked as a flight director and then as a senior leader of the Space Shuttle program.
In this interview, we discuss how long the company's current spacecraft, VSS Unity, can keep flying, plans to introduce a new Delta-class family of spaceships, and why there probably will always be pilots at the controls of Virgin Galactic. This conversation has been edited lightly for clarity.
Ars: You came to Virgin Galactic in 2011. Can you tell me a little about your decision to leave NASA? Was it because the shuttle program was over but you wanted to continue to do human spaceflight?
Mike Moses: That's kind of it in a nutshell. It was an honor and a privilege to be there at the end of the shuttle program and kind of lead that team through. Bittersweet to be closing it out, but we know we finished strong, and everything went really, really well. I was contemplating what was next.
I was probably going to head up to headquarters with Gerst [NASA Associate Administrator Bill Gerstenmaier] and Bill Hill and work on what is now Artemis. And when I looked at that—it was a long way away, even back then, when they were being very optimistic with the pacings. I just wanted to keep doing operations. I had a very big heart-to-heart conversation with Gerstenmaier, and he didn't push me out the door, but he said, 'Don't feel bad about leaving. You're going to do as much for commercial space as you would if you stayed here. Take these lessons and go.' That was the little confidence boost I needed to make the switch into commercial space.
Ars: What do you think about the commercial space industry at the time?
Mike Moses: Back then, they were just getting ready with Commercial Crew. They [commercial providers SpaceX and Orbital Sciences] hadn't even flown cargo yet. So that's where the suborbital market was, and I thought they would probably be the first ones to make it, before the orbital stuff. It turns out that's not the way it played out.
Anyway, I contemplated that and felt if I was gonna stick around and do orbital stuff, I would have probably stayed at NASA for it. This was a chance to come try something that really is about giving people experiences. In the government, that's not really what you do, right? You're doing a service. So it was kind of a unique challenge for me. I think I was the sixth employee in the operations team. We had a procurement person, a safety person, and a medical person in, then me. I was going to help build it from scratch, and that was a huge appeal to me.
Ars: So it's been 12 years. From an engineering standpoint, what has been the biggest challenge of getting a relatively small vehicle to space and back?
Mike Moses: One of our challenges is the air launch capability. It's a great benefit of our system, but we have to be very careful with it. We transition through a large number of flight regimes. If you think about it as an airplane, we separate away; we're very heavy when we release Unity from the Mothership. And we're subsonic with a very back-heavy center of gravity when we light the motor. We're basically like any rocket in that we're half propellant.
Within 60 seconds, we've lost half our weight, we transition supersonic, we go vertical, and now we're on our tail. Then, when we come back down, you've got to break the sound barrier. You're in a feathered configuration, and now you're a very light, forward center-of-gravity aircraft. To optimize the flight-control systems, to be able to handle all of those regimes, you really have to get some flight test data in each of them and then put it together and optimize.
We had laid out some plans and we had options, but we really didn't know how fast it was going to go until we started getting that data. And that turning of the vertical is not as simple as you might think it is. You have to balance Mach numbers, angles of attack, air speeds, flutter considerations, and all of that stuff. We had to dial that in, and that took us a little while. It didn't help with the accident, and we had some damage along the way that we had to repair. That kind of slowed us down a bit.
I think our biggest technical challenge at the beginning of the program was getting the rocket motor dialed in with Scaled Composites. And then, for us, it was basically exploring that transonic flight envelope. Most rockets just punch straight through it. They don't have to try to fly and maneuver as they're going transonic. Again, I love this system, and that's its most complicated part, and we wanted to make sure we got it right.
Ars: When were you doing a lot of that work?
Mike Moses: In 2017 and 2018, we were finishing our glide program and our partial duration burns. We flew about four or five flights with less than full-duration burns of the motor that were non-space flights. That's where we were intentionally getting into that transonic envelope at different configurations to try to gather the data. Then we put it together, went to space in 2018, and went to space in 2019, and we were ready to tune it. We had some damage to the ship that took us a while to replace the H-stabs (horizontal stabilizers). That kind of slowed the program down again, and then we picked back up. And then we started flying again after COVID.
Ars: Based on what you know now, what is your confidence in the life span of VSS Unity?
Mike Moses: Pretty highly confident. One of the nice things about this is we now know its envelope, and we fly in that envelope. Our controllability and our reliability in that envelope is really high, and it's one of the things that's enabling us to turn frequently. We're flying once a month because I fly the profile I flew last time. So I can look at the data, look at the trajectories, look at the temperatures, and they're exactly what they were. We just do it again and again. Basically, you design a vehicle to be operating out here, you've tested here, and then you actually fly it here, and that's what we're doing right now. We're just staying right in this soda straw and flying, and it's performing really, really well.
Ars: But the Space Shuttle obviously had lots of wear and tear. Of course, they were going to orbit for a couple of weeks and back. But the Falcon 9 goes up and flies again. It's got wear and tear. So, from a life-span perspective, how many missions do see with this airframe?
Mike Moses: We actually think it's 500 to 1,000. It's a 10-year life span. We designed for 10 years, flying once a week, so that's roughly 1,000 flights. The new Delta fleet will be the same, a 10-year life span. When you talk about reusability, Dragon is doing amazing things, and Falcon is doing amazing things. They're still in the 10s and 20s, and we're shooting for hundreds and hundreds of flights.
There are going to be parts that wear out, that we've got to replace, and we've designed for that. You know, a lot of the metallics, you want to look for fatigue and change them out after so many flights. But the carbon fiber is really meant to be that durable. And it's one of the reasons that the mod period [modifications to VSS Unity and the Mothership VMS Eve from mid-2021 to early-2023] was both a blessing and a curse. We needed it to beef up the system so that we don't have to look at the vehicles every time. So we get that reliability of a fatigue life. But it took us longer to complete than we meant, so we were out of the flight test world for a while there. Obviously, we would have liked that to grow faster, but it did what it was supposed to do. Some places I can now inspect after every five flights instead of every flight.
Ars: What are like the major changes that are being made to the Delta-class ships to make them more manufacturable?
Mike Moses: One is manufacturing. When we laid up Unity and Imagine, you have a mold tool, and you lay down the carbon fiber, bake it in the oven, then take that part out and bond it to another one. Each tool became the fitting for the next one. You build a lower wing skin, and then you'd go build the ribs and glue them in the lower wing skin tool. You were basically assembling like if you were building a Lego Star Destroyer. Layer by layer, you build the ship. Delta-class is going to be built in modules. So there will be a forward fuselage, an aft wing, and a feather. You make those things in their own jigs, and they'll come together as one unit. And it's much more like how airlines assemble their planes—modular build-to-print, plug-and-play fittings. If you're only going to make two or three spaceships, you wouldn't invest in that type of manufacturing ability. We want to make a couple dozen.
Ars: What gives you confidence that the Delta ships will be able to fly weekly?
Mike Moses: The maintenance. Right now, on Unity, if I need to do some inspections behind the main oxidizer access panel, it's a big giant panel that's got 35 fasteners, which sometimes get stripped and then have to be replaced. It's very labor intensive because it wasn't built for this. On an airplane, there would be three quick-turn fasteners. A panel comes off, and it goes right back on again.
Delta is going to have that stuff built in. The ships also have critical joints. Unity is glued together; it has bonded joints. On Delta, we'll have them fastened with fasteners. Again, from an inspection perspective, I don't have to go bring an X-ray scanner in and determine the health of the glue joint. I have fasteners that have life on them, and I just have to know when I need to check them. It's much faster, and that's what gives us the confidence in the weekly turn rates for Delta.
If you apply that to Unity, we'd be able to turn it weekly as well. With the ship itself, things like loading a rocket motor or mating it to the Mothership—all that stuff supports a three-day turn even on Unity. It's the fact that I have to go inspect bonded joints in the wings that takes time. Somebody has to physically go in [and] bring an ultrasound scanner or an X-ray machine. We don't have to do it every flight, but we do it a lot. It's our fleet leader, and we want to be looking at it.
Ars: When do you plan to begin manufacturing the Delta ships?
Mike Moses: The tooling is being built now. Parts will start coming out by the end of this year, sub-component parts at the vendors. Major assemblies are being delivered, I think, at the middle to end of 2024, and then final assembly in 2025. Were showing first-flight capability at the end of 2025 and then moving into flight test and then into commercial service in 2026.
The benefit there is that we're keeping the same outer mold line, so I already know my aerodynamics, my loads, the thermal, all of that stuff, it's all set, I don't have to go learn it again. The structure underneath it, I'm going to change, but what it's reacting to externally, I already know. Whereas if I was starting clean sheet, making that timeline I just told you, you would be a little skeptical, right? But we already know the environment we're about to put it in, and that's a huge benefit to us.
Ars: How much of the engine is reusable, and how much do you have to replace?
Mike Moses: We have helium and oxygen, nitrogen, and other gases on board. You obviously have to fill those back up. The nitrous oxide tank is liquid, so we have to refill that every time, but it's a reusable composite overwrapped pressure vessel, so the tank itself is reusable.
The rocket motor cartridge, the fuel, is the only thing we change out every time. It's a lot like an Estes motor rocket. It's a casing that has solid fuel poured into it. We wrap it with a rubber bladder and then wrap it with Kevlar and carbon fiber to give it structure. The nozzle is integral to the back of it. That whole thing is one use. You burn it from the inside, out to the outside of the case, and the nozzle is ablative and sheds material to dump heat. It's not reusable at that point. It takes us about four hours to take an old motor out and put a new one in, so it's not that hard to change one out. Currently, we make them two to three a month. There is a high cost per unit because we're using our research and development test stand.
But we've laid out a new set of test stands in Mojave, where we can make about 20 motors a month if we need to. When we get to the Delta class, we're going to need to build a bigger facility. We're going to do more of an assembly line, and then the unit cost per motor just drops dramatically at that point. It's not that expensive, and it's not that labor-intensive. And to be honest, from a consumer perspective, I really love that it's a very durable, simple system. I have six of them stored out here in the hangar, and they're not a hazard.
It's just simple and plain, but that's a good thing in a consumer product. I call it a station wagon. Richard (Branson) likes to talk about it being a sports car. It's a station wagon. I just want it to do simple, reliable things regularly. You're not going to go to the Moon on a hybrid rocket motor. You're not going to go to Space Station on a hybrid rocket motor. But you want to do suborbital tourism? It's a really great choice for that.
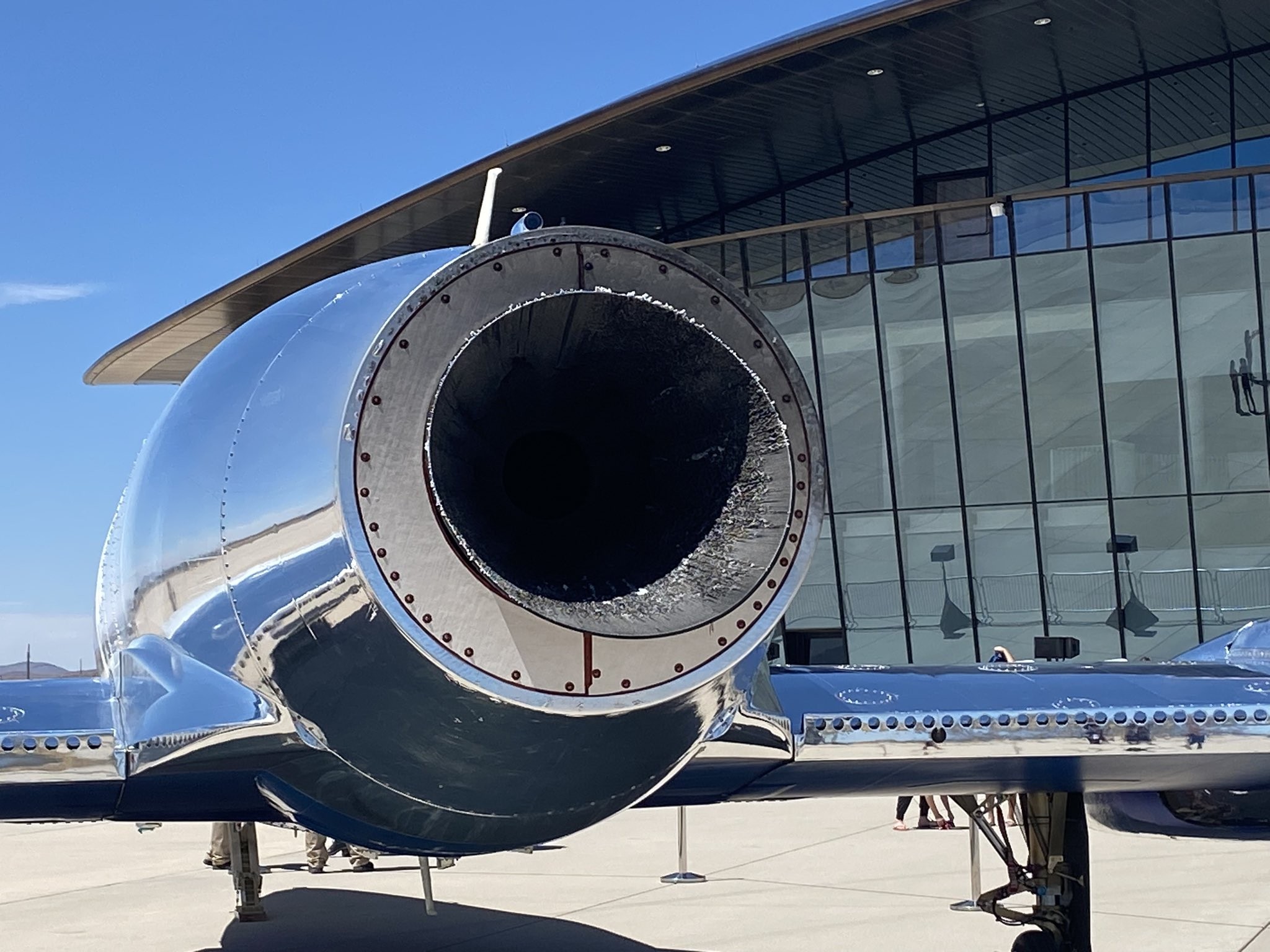
Ars: How many more Motherships do you think you're going to need?
Mike Moses: Let's say our goal is to fly daily. We round that up and say 400 flights a year. Everybody asks where we got the 400. Just take 365 and round up. So once-a-day operations, plus a couple extra. If a spaceship can turn on three to five days, I need probably four to eight of those, so I have one ready every day. A Mothership can turn every other day, so I probably need two Motherships alternating in parallel. Three would be nice to have. We basically need two flying Motherships, and that's the model to be able to handle daily flight. That requires a mothership that can fly a little more frequently than Eve.
Ars: I've heard there are some pretty high maintenance requirements for Eve.
Mike Moses: We've done a lot of work on that. The mod period was mostly focused on Eve. Unity got some work, but most of it was aimed at Eve. We're on roughly weekly centers with Eve now, and we have more work planned [meaning] that we can get a little better than that. Then we'll be building new Motherships that will be able to do more and more reliable flights. Our biggest challenge with Eve is that it was built back in 2008. At the time, it was the largest all-composite aircraft, and some of those lessons learned are still in it.
Ars: I don't think these vehicles were optimized for reuse, were they?
Mike Moses: They weren't optimized for that. We've been modifying them over the years... Folks who come to our company [often] say the same thing, that Scaled Composites built these vehicles as prototypes. Yes. But we spent the last 10 years changing it from a prototype into a low-rate operational vehicle. That was the point of all the maintenance we've been doing on them.
Ars: You've obviously got a great group of pilots. And coming from the shuttle program, I'm sure you have great confidence in the people flying the vehicles. But we're in an industry now that's moving toward automation. New Shepherd and Crew Dragon are automated. I could go to orbit in Dragon, I think. The astronauts don't touch it. But it seems like you're putting a lot on your pilots every flight. Is that sustainable?
Mike Moses: It's a really good question. In the model of keeping everything simple and redundant and reliable—those initial prototype vehicles, you want them human-flown. Because you're not exactly sure what environment you're going to see in a test program. Going back to pros and cons, it's great to have a human-flown vehicle. That means the very first flight has to have humans on it. The system had to be very reliable back then, so it was a high workload at the time.
Now that we've dialed it in, we've been slowly making changes to the flight control systems. We spend most of our energy not on automation but on information display and simplicity of guidance to the pilot. They get simple guidance on what to do, with simple actions they can take from that based on the flight test history. Just the way we turn into that gamma turn—there are actuators out there that drive the H-stabs up and down. During the last down period, we doubled the size of the motors, and we can drive them much faster. The pilots make less inputs, so there's less variability in what they do.
We have also changed some of the energy display so they have better details. We keep making little tweaks like that. I have very high confidence in it because we were driving that workload lower. Eventually, we will start adding digital systems, kind of like Shuttle had, so I could say, "wings level hold," and an autopilot would do that. We don't have it right now, but we have all the systems in place that we can activate in the future with some software upgrades.
We're adding in the ability to kind of bootstrap once we've gathered enough flight data and can move that into a more automated system. I don't think we'll ever go pilot-less. There's a huge benefit, I think, in a consumer product to having people with you. You get to go to space together. You're part of a crew. You have confidence in that crew. We have very highly trained pilots. We'll probably keep that for quite a while. I don't think I'll run out of people who are willing to fly the spaceship any time soon.
Recommended Comments
There are no comments to display.
Join the conversation
You can post now and register later. If you have an account, sign in now to post with your account.
Note: Your post will require moderator approval before it will be visible.