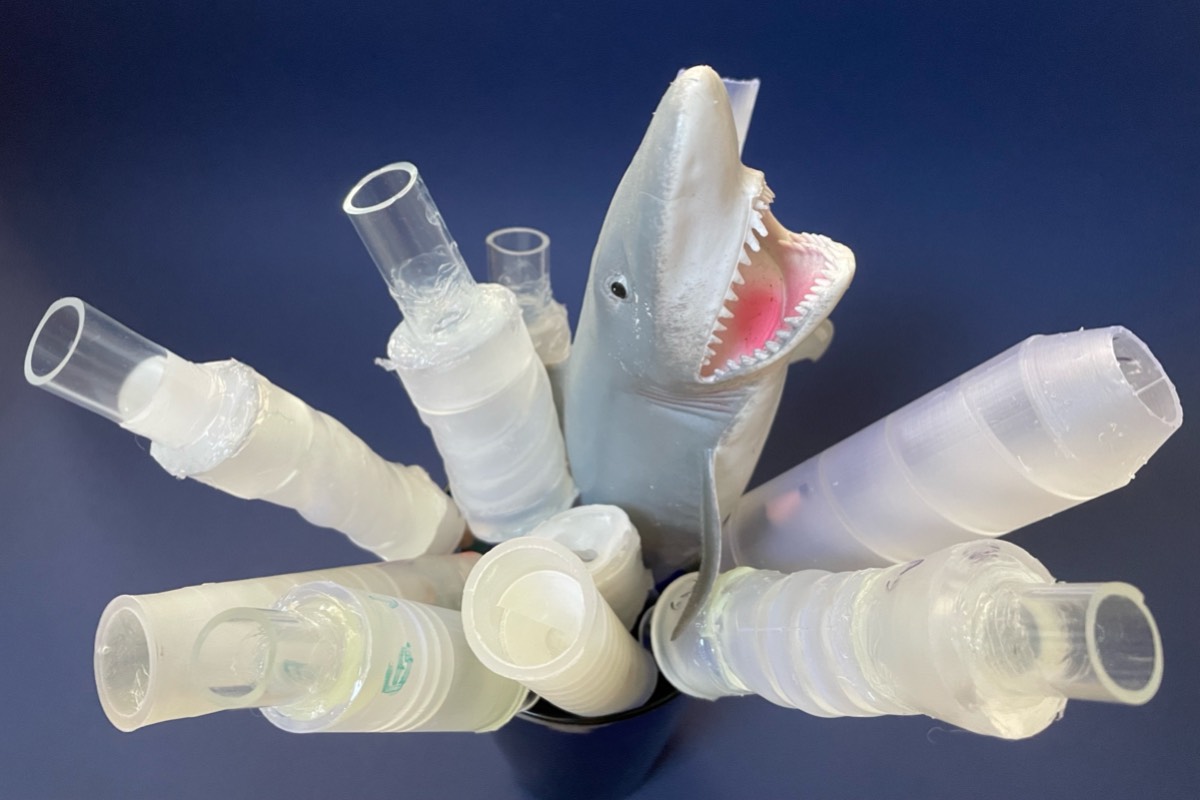
Scientists at the University of Washington have re-created the distinctive spiral shapes of shark intestines in 3D-printed pipes in order to study the unique fluid flow inside the spirals. Their prototypes kept fluids flowing in one preferred direction with no need for flaps to control that flow and performed significantly better than so-called "Tesla valves," particularly when made of soft polymers, according to a new paper published in the Proceedings of the National Academy of Sciences.
As we've reported previously, in 1920, Serbian-born inventor Nikola Tesla designed and patented what he called a "valvular conduit": a pipe whose internal design ensures that fluid will flow in one preferred direction, with no need for moving parts, making it ideal for microfluidics applications, among other uses. The key to Tesla's ingenious valve design is a set of interconnected, asymmetric, tear-shaped loops.
In his patent application, Tesla described this series of 11 flow-control segments as being made of "enlargements, recessions, projections, baffles, or buckets which, while offering virtually no resistance to the passage of fluid in one direction, other than surface friction, constitute an almost impassable barrier to its flow in the opposite direction." And because it achieves this with no moving parts, a Tesla valve is much more resistant to the wear and tear of frequent operation.
Tesla claimed that water would flow through his valve 200 times slower in one direction than another, which may have been an exaggeration. A team of scientists at New York University built a working Tesla valve in 2021, in accordance with the inventor's design, and tested that claim by measuring the flow of water through the valve in both directions at various pressures. The scientists found the water only flowed about two times slower in the nonpreferred direction.
Flow rate proved to be a critical factor. The valve offered very little resistance at slow flow rates, but once that rate increased above a certain threshold, the valve's resistance would increase as well, generating turbulent flows in the reverse direction, thereby "plugging" the pipe with vortices and disruptive currents. So it actually works more like a switch and can also help smooth out pulsing flows, akin to how AC/DC converters turn alternating currents into direct currents. That may even have been Tesla's original intent in designing the valve, given that his biggest claim to fame is inventing both the AC motor and an AC/DC converter.
It helps to be a shark
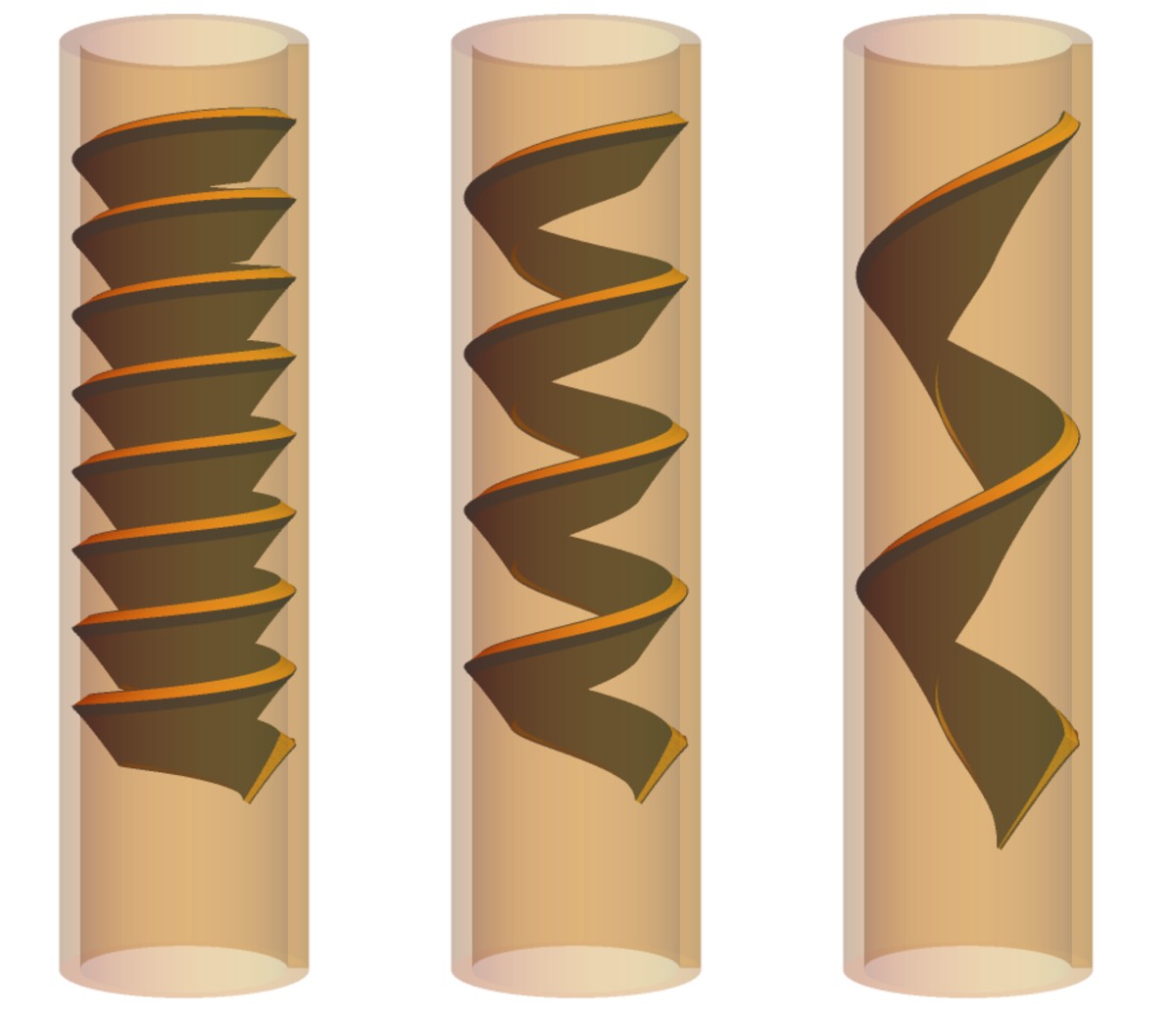
The Tesla valve also provides a useful model for how food moves through the digestive system of many species of shark. In 2020, Japanese researchers reconstructed micrographs of histological sections from a species of catshark into a three-dimensional model, offering a tantalizing glimpse of the anatomy of a scroll-type spiral intestine. The following year, scientists took CT scans of shark intestines and concluded that the intestines are naturally occurring Tesla valves.
That's where the work of UW postdoc Ido Levin and his co-authors comes in. They had questions about the 2021 research in particular. "Flow asymmetry in a pipe with no moving flaps has tremendous technological potential, but the mechanism was puzzling,” said Levin. “It was not clear which parts of the shark’s intestinal structure contributed to the asymmetry and which served only to increase the surface area for nutrient uptake.”
Levin et al. 3D-printed several pipes with an internal helical structure mimicking that of shark intestines, varying certain geometrical parameters like the number of turns or the pitch angle of the helix. It was admittedly an idealized structure, so the team was delighted when the first batch, made from rigid materials, produced the hoped-for flow asymmetry. After further fine-tuning of the parameters, the rigid printed pipes produced flow asymmetries that matched or exceeded Tesla valves.
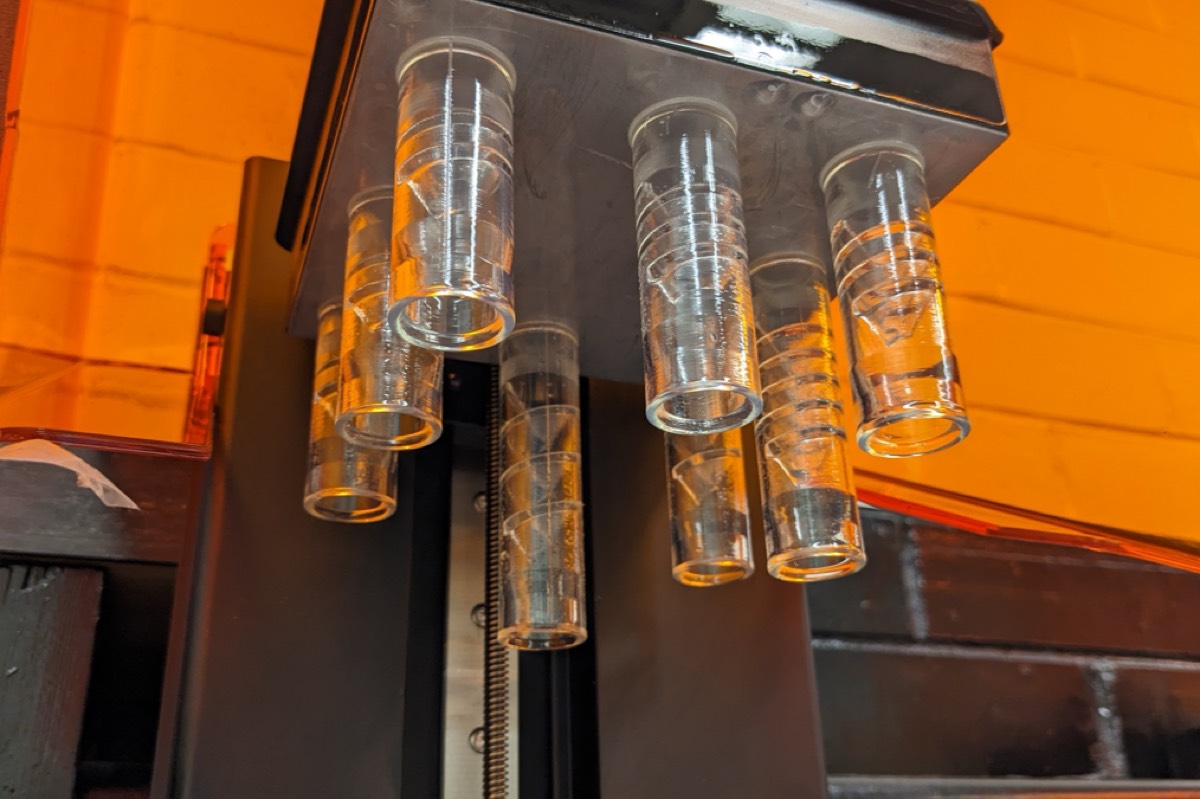
But the researchers weren't done yet. "[Prior work] showed that if you connect these intestines in the same direction as a digestive tract, you get a faster flow of fluid than if you connect them the other way around. We thought this was very interesting from a physics perspective," said Levin last year while presenting preliminary results at the 67th Annual Biophysical Society Meeting. "One of the theorems in physics actually states that if you take a pipe, and you flow fluid very slowly through it, you have the same flow if you invert it. So we were very surprised to see experiments that contradict the theory. But then you remember that the intestines are not made out of steel—they’re made of something soft, so while fluid flows through the pipe, it deforms it.”
That gave Levin et al. the idea to try making their pipes out of soft deformable polymers—the softest commercially available ones that could also be used for 3D printing. That batch of pipes performed seven times better on flow asymmetry than any prior measurements of Tesla valves. And since actual shark intestines are about 100 times softer than the polymers they used, the team thinks they can achieve even better performance, perhaps with hydrogels when they become more widely available as 3D printing continues to evolve. The biggest challenge, per the authors, is finding soft materials that can withstand high deformations.
Finally, because the pipes are three-dimensional, they can accommodate larger fluid volumes, opening up applications in larger commercial devices. “Chemists were already motivated to develop polymers that are simultaneously soft, strong and printable,” said co-author Alshakim Nelson, whose expertise lies in developing new types of polymers. “The potential use of these polymers to control flow in applications ranging from engineering to medicine strengthens that motivation.”
PNAS, 2024. DOI: 10.1073/pnas.2406481121 (About DOIs).
Recommended Comments
There are no comments to display.
Join the conversation
You can post now and register later. If you have an account, sign in now to post with your account.
Note: Your post will require moderator approval before it will be visible.